I’m not one for resolutions, but as a new year is almost upon us, it’s time to reflect on all of the good things that happened in 2024. There are many, many applications for 3D printing, but today we’re focusing on five heartwarming examples of how the technology was used this past year to help animals.
Protecting Fairy Tern Eggs with 3D Printed Replicas
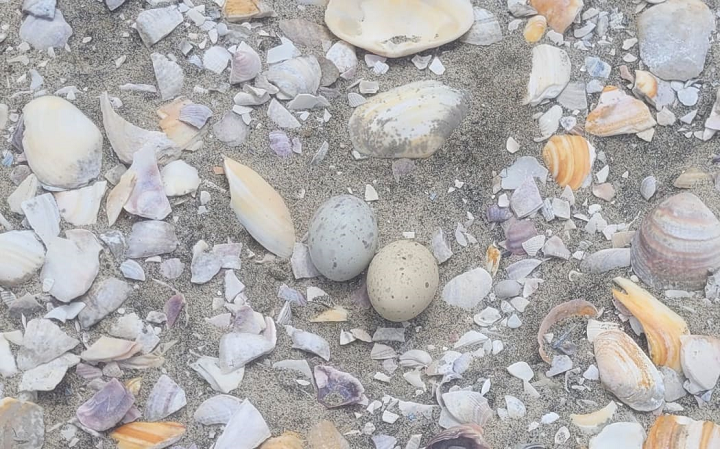
Fairy tern/tara iti egg (L) and 3D printed dummy egg (R) used in the nest protection program. Photo: Supplied / DOC
The once-widespread fairy tern, or tara iti, is New Zealand’s rarest indigenous breeding bird, according to the ZSL institute of Zoology. This small, coastal bird lays its eggs on sandy beaches with little protective vegetation, and there are only a few remaining breeding sites, all of which are vulnerable to threats like storms, beach development, and predators. But the Department of Conservation (DOC) in New Zealand, which began conservation management for the tara iti many years ago, is now using 3D printing to help protect the eggs of this extremely endangered bird.
During high-risk periods, DOC staff takes eggs from the fairy tern nests and replaces them with fake ones. The real eggs go into incubators at the Auckland Zoo, while the replicas give the birds something to incubate themselves. Initially, hand-painted wooden eggs were used, and then real eggs with wax inside the hollow center. But thanks to funding from the Endangered Species Foundation (ESF) – Tāngaro Tuia te Ora, the DOC was able to commission the creation of 3D printed replica eggs. Because the 3D printed eggs match the real ones in size, color, texture, shape, weight, and UV resistance, the birds didn’t even realize that they’ve been swapped. The initiative reported a record-breaking breeding season with 22 eggs laid and 14 chicks hatched, so clearly the 3D printed replica eggs are working!
Polly the Pekin Duck Gets 3D Printed Prosthetic Bill
A wildlife rehabilitation center in Texas helped over 4,000 animals this year, including a resilient Pekin duck named Polly. In late 2023, Polly was found with a badly damaged bill and brought to All Things Wild. Likely the result of a predator attack, the injury affected Polly’s ability to preen and maintain her feathers, though the unflappable bird adapted remarkably well. Still, in order to restore the duck’s quality of life, the team at the center proposed the idea of a 3D printed prosthetic bill for Polly, which resulted in a heartwarming joint effort between wildlife caretakers and the academic community.
Dr. Laura Hobgood of Southwestern University and her students began the project that, as Editor-in-Chief Michael Molitch-Hou wrote in April, “could set a precedent for future wildlife rehabilitation efforts.” Their goal was to design and fabricate a fully mobile replacement beak that would attach seamlessly to Polly’s damaged one, so she could regain 100% functionality. Polly, and some other similar ducks, were 3D scanned in order to create a workable 3D model that would lead to a perfectly fitted bill. While the team was working on the 3D printed prosthetic bill, the local community rallied around the resilient Polly, raising money for her care, as well as the needs of other animals at All Things Wild.
Metal 3D Printed Cast for Zoo Gorilla’s Broken Arm
Gladys, an 11-year-old gorilla who lives at the Cincinnati Zoo & Botanical Gardens, suffered a broken arm during a scuffle with some of her friends. The zoo staff collaborated with local anesthesiologists and surgeons to fix her up, and the surgery was successful. However, the team thought a sturdier cast was needed. Gladys was obviously curious about the strange thing on her arm, and as Cincinnati Zoo’s Director of Animal Health Dr. Mike Wenninger explained, she didn’t “fully understand the need to preserve it for her recovery.” So they called on Colibrium Additive (formerly GE Additive), which is also based in Cincinnati, Ohio and had previously worked with the zoo.
The company partnered with the zookeepers to build a 3D printed cast for Gladys. Colibrium Additive engineers used the scans of the young gorilla’s first cast to design a new one, and within a week, a stronger cast had been 3D printed out of titanium. The cast was made up of two parts, which were printed in about 65 hours, and weighed about eight pounds. The goal of this 3D printed metal cast was actually to give the gorilla more freedom—when wearing the first cast, there were some zoo spaces that were unsafe for her to visit. But with this titanium upgrade, Gladys was able to go back to exploring additional behind-the-scenes spaces.
WIMBA’s Partnership & New 3D Printing Facility
This spring, Polish startup WIMBA announced a partnership with top Italian orthopedic solutions provider Intrauma to advance veterinary care with 3D printed orthotics. WIMBA uses HP’s Multi Jet Fusion 3D printing to make lightweight, custom-fit pet orthotics, while Intrauma manufactures a range of internal fixators, and its VET LINE develops everything from osteotomy instruments to orthopedic suture systems. The goal of this partnership was to improve pet orthopedics with custom orthotics, and bring 3D printed animal medical devices into the mainstream. Both companies share a passion for animal welfare, and their work could result in medically validated tools, lower costs, shorter production times, and an easier experience for veterinarians, pets, and their owners.
Its work with Intrauma wasn’t WIMBA’s only big news this year—the startup also opened a new in-house 3D printing facility in its Kraków headquarters a few months ago. By making a strategic investment into this new facility, WIMBA brought production onsite, which allows it to ensure excellent quality control, enable a much faster turnaround time for custom pet orthotics and prosthetics, and create more tailored mobility outcomes. The facility’s in-house processes include 3D printing, cooling, and sandblasting, which allows WIMBA “to deliver most standard orthotics within just 10 working days,” according to co-founder and CEO Greg Kosch.
3D Printed Harness for Turtle with Bubble Butt Syndrome
While it may sound like a joke, bubble butt syndrome is a debilitating condition that afflicts many sea turtles by causing air pockets, or bubbles, in their shells. This makes it challenging for the turtles to swim naturally, as they end up tilted at odd angles and unable to fully submerge. Back in 2008, Mystic Aquarium in Connecticut rescued a green sea turtle named Charlotte who was suffering from this condition after being struck by a boat. Last month, after years of collaborative effort, the male turtle was fitted with a custom 3D printed harness to help him swim normally and regain his quality of life. The aquarium partnered with additive manufacturing solutions firm Adia, 3D printer manufacturer Formlabs, and the computational design team at New Balance Athletics for this project.
The team spent five years refining the design, and several prototypes were built and tested for functionality, durability, and comfort. The Formlabs Fuse 1 SLS 3D printer was ultimately used to produce the device out of a special carbon fiber-reinforced Nylon 11. Thanks to a weight system that handlers can adjust as the air bubble in Charlotte’s shell shifts, the final harness design will ensure that the turtle’s swimming posture is stable. The implications of this project could be widespread—both New Balance and Mystic Aquarium presented findings at industry conferences, which has resulted in interest from aquariums around the U.S. New Balance is now building a computational pipeline to streamline design and production of customized sea turtle harnesses, and was joined by Adia in issuing a call for volunteers with expertise in 3D printing, computational design, and materials science to join their life-saving efforts.